We will show you what is behind point clouds, why they are indispensable in industry and what you can use point clouds for.
Digitized and automated production is almost inconceivable without point clouds. Where CAD-models represent the digitally developed ideal image of an object, point clouds bring users and decision-makers back down to earth. Because the digital image follows exactly the lines, dimensions and edges actually found in reality.
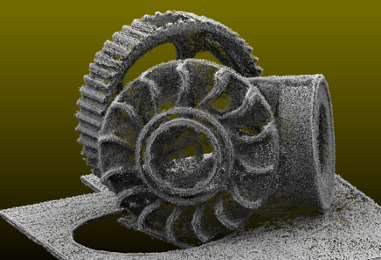
In concrete terms, a point cloud describes the set of points in a vector space. These have an unorganized structure, which is why the points are also called a “cloud”. Only the multiplicity of individual points leads to the fact that a point cloud becomes a form. In addition to spatial coordinates, the points of such a cloud can also store the color and light intensity of a measurement point. This allows point clouds to show additional details.
However, if you zoom in very close to a point cloud, you will quickly notice that the points initially remain unconnected. The model created from the point cloud is full of holes. For an optimal 3D model, a close-meshed recording of points is necessary – and very good rendering software.
But even to display point clouds, you need your own visualization programs. The most popular open source versions include:
- CloudCompare
- Meshlab
- GOM Inspect
In contrast to professional solutions like Point Cloud Library (PCL) they offer only limited processing of point clouds. However, they are sufficient for object viewing and estimating point cloud quality.
But how are objects created from points?
Points for a point cloud are created in particular by optical scanning. Here, a distinction is made between two processes:
- Triangulation using laser technology: Here, the angle of the reflected laser beam allows the calculation of the individual coordinates.
- Normal light scanner: Using structured light, the software precisely calculates coordinates of individual points from the image.
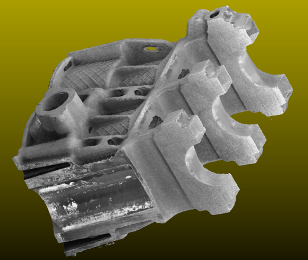
Only when as many points as possible have been recorded, as accurately as possible, can the actual object be created from them. The derivation of objects from this number of points works by means of 3D rendering. In this process, the software combines individual points into polygons, which in turn form a surface. Various algorithmic processes such as wireframes, scanlining or radiosity then help to smooth edges and output a uniform, realistic appearance.
So what are point clouds for?
Due to their catchy principle of object mapping, point clouds offer the optimal basis for digitizing objects together with their actual properties. In addition to modeling and planning further production steps, point clouds also allow automated processing of scanned objects. This is because ideal CAD models often do not sufficiently match their real counterparts. If the precision of the image matches, a point cloud depicts the actual object much more accurately.
This advantage can be used for automated quality inspection, for example. With the point cloud, a system detects unwanted deviations and can sort out the corresponding part. In addition, point clouds can also be used for predictive maintenance. Material wear or brittleness often announce themselves before the defect occurs. With a point cloud, such small changes can be detected at an early stage.
This shows that a single point may not yet have much effect, but many points together result in new, exciting fields of application for industry. What do you use point clouds for?