Der Einsatz von Robotern in der Industrie birgt viele Vorteile. Durch ihre Nutzung beschleunigen sich Prozesse, sie werden präziser und Anlagen können 24/7 laufen. Um Roboter in die Produktionslinie zu integrieren, sind Anlagenbauer gezwungen, fehlendes Roboterwissen hausintern aufzubauen oder extern einzukaufen. Wichtige Fragen dabei sind: Welcher Roboter ist der Richtige? Wer kann den Roboter in Betrieb nehmen? Wie viele Roboter können verwendet werden? Fehlendes Roboter-Know-how lässt sich mit Hilfe der Programmierung über eine speicherprogrammierbare Steuerung (SPS) ausgleichen und macht die mühsame Abstimmung zwischen Roboterspezialist und Programmierer überflüssig.
Wie ist eine SPS aufgebaut?
SPS ist eine Programm(-ier)-Komponente, um eine Anlage oder Maschine zu regeln bzw. zu steuern. Somit sind wiederholbare Prozesse wie die Steuerung einer automatisierten Produktion, Ampelanlage oder einer Kläranlage einfach durchzuführen. Eine SPS besteht aus Eingängen, Ausgängen, einem Betriebssystem (Firmware) und einer Schnittstelle, über die das Anwenderprogramm geladen werden kann.
Das Anwenderprogramm legt fest, wie die Ausgänge in Abhängigkeit von den Eingängen geschaltet werden sollen. Das Betriebssystem hingegen stellt sicher, dass dem Anwenderprogramm immer der aktuelle Zustand der Geber zur Verfügung steht. Durch diese Informationen schaltet das Anwenderprogramm die Ausgänge so, dass die Anlage in der gewünschten Weise funktioniert. Durch Sensoren und Aktoren gelingt die Anbindung der SPS an die Maschine bzw. Anlage. Sensoren sind an die Eingänge der SPS geschaltet und vermitteln das Geschehen in der Maschine oder Anlage. Beispiele hierfür sind:
- Bilder/Punktwolken,
- Taster,
- Lichtschranken,
- Inkrementalgeber (Sensor zu Erfassung der Lage- oder Winkeländerung),
- Endschalter,
- Temperaturfühler, oder
- Füllstandsensoren.
Aktoren hingegen sind an die Ausgänge angeschlossen und bieten die Möglichkeit, die Maschine oder Anlage zu steuern. Beispiele für diese sind:
- Schütze zum Einschalten von Elektromotoren,
- elektrischen Ventile für Hydraulik oder Druckluft oder
- Module für die Antriebssteuerung.
Sensoren und Aktoren werden immer häufiger mit der SPS über Feldbus und nicht mehr diskret verbunden. Dadurch verringert sich der Verdrahtungsaufwand enorm.
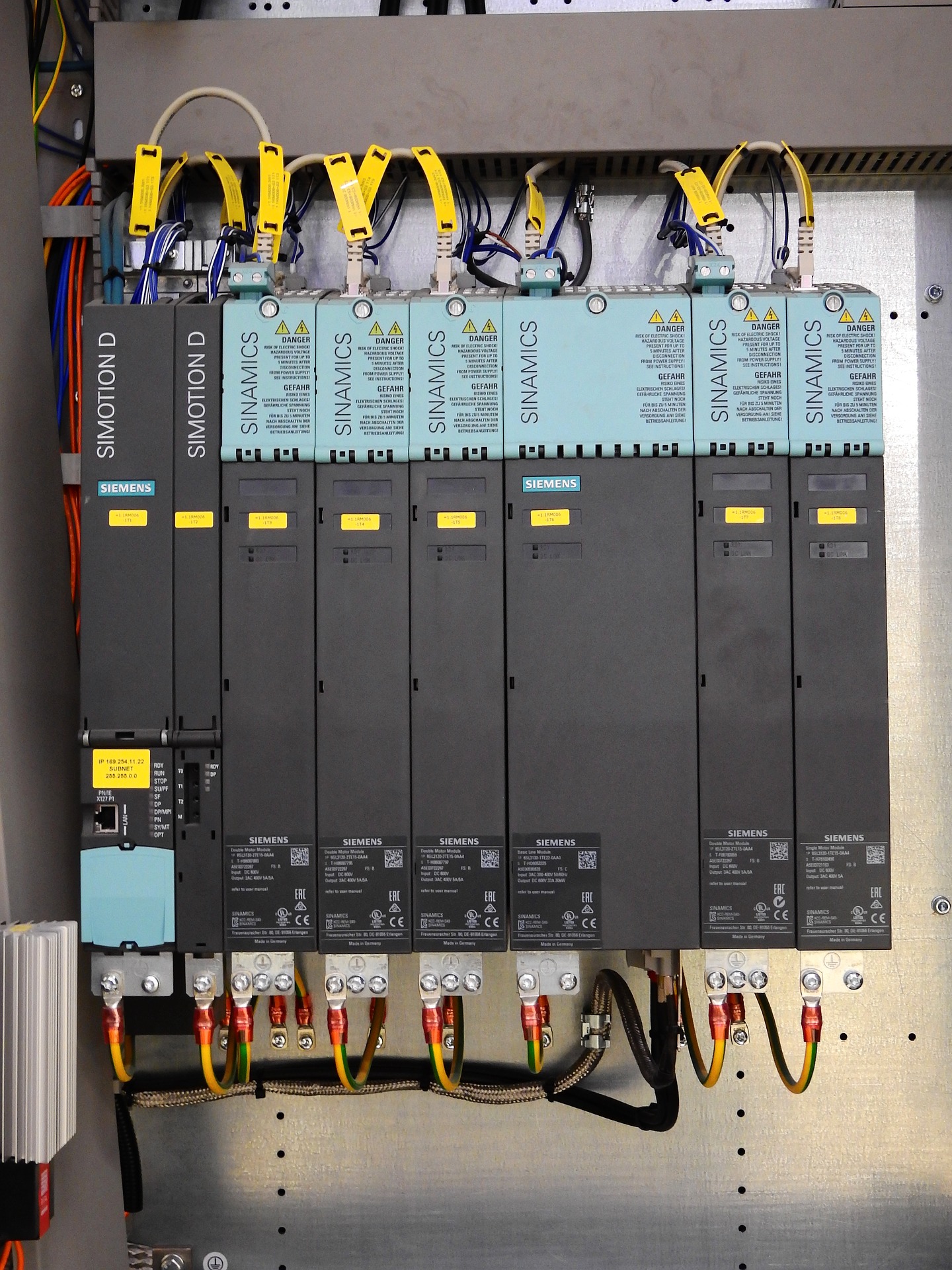
Aufbau einer SPS
Herausforderungen ohne SPS
Ohne SPS gibt es aus Entwicklersicht zwei Kategorien: Roboterprogrammierer und Softwareprogrammierer. Beide Teams entwickeln für ihre Bereiche die jeweiligen Ablaufprogramme, sowie Mensch-Maschinen-Schnittstellen. Durch diese Visualisierungen ist es möglich, die Anlagenabschnitte zu bedienen.
Trotz hoher Verfügbarkeit der Anlage kann es hin und wieder zu Störungen und somit zu Anlagenstillständen kommen. In der Regel besitzt ein Anwenderunternehmen wenig Roboter-Know-how, aber häufig ein Instandhaltungsteam mit SPS-Programmiererfahrung. Ist der Anlagenbediener nicht selbst in der Lage, den Fehler zu lokalisieren und so die Störung zu beseitigen, zieht er zuerst die firmeninterne Instandhaltung zu Hilfe. Wenn diese allerdings keinen Erfolg haben, muss die Firma einen externer Roboterspezialisten ordern. Dies kann unter Umständen einen längeren Anlagen- und damit einen Produktionsstillstand bedeuten.
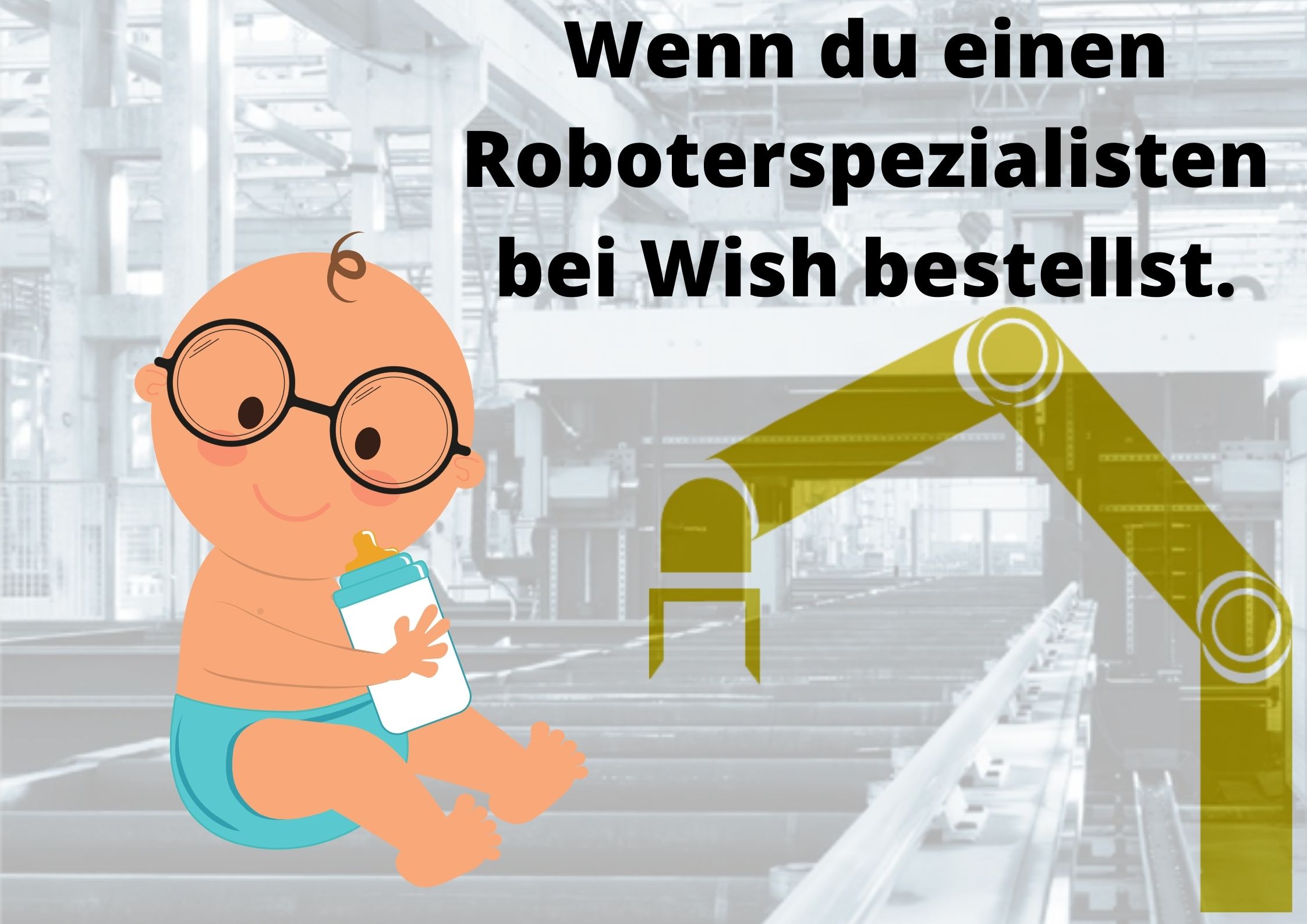
Unklare Zuständigkeiten und fehlende Absprachen behindern oftmals die Suche nach der Fehlerursache. Nicht nur während der Projektierungs-, der Programmier- und der Inbetriebnahme-Phase kommt es zu Reibungspunkten. Auch während der Gewährleistung führen getrennte Teams häufig zu Mehraufwänden, was im Endeffekt die Effizienz schmälert.
Selbst wenn ein Anlagenlieferant einen passenden Partner mit Roboter-Know-how gefunden hat, der auch im Supportfall gut unterstützt, reicht dies nicht aus. Ein weiterer Kundenanspruch führt ebenfalls zu neuen Herausforderungen: Kunden verlangen mehr Flexibilität bei der Auswahl des Roboterherstellers.
Roboterprogrammierung mit SPS-Entwicklungsumgebung
Die Lösung ist eine SPS
Zwei Kunden haben ein BinPicking-Problem zu lösen, arbeiten aber mit Robotern von unterschiedlichen Herstellern. Dadurch unterscheiden sich die Entwicklungsumgebungen der beiden Projekte erheblich. Um diese Problematik zu lösen, bräuchte ein Anlagenlieferant für beide Kunden entweder unterschiedliche Roboterspezialisten oder er verwendet eine SPS.
Durch diese ist der Anlagenlieferant in der Lage, in einer gewohnten SPS-Entwicklungsumgebung mit Hilfe einer Roboter-Befehls-Bibliothek den Roboter selbst zu programmieren. Er benötigt immer noch Hilfe bei der Planung (Auswahl des richtigen Roboters), sowie bei der Grundinbetriebnahme (Installation Robotersoftware, Einrichtung der Arbeitsräum, Vermessen der Werkzeuge). Dieser Aufwand ist aber sowohl zeitlich als auch kostentechnisch gesehen relativ gering.
Mit der SPS übernimmt der Anlagenlieferant selbst die Inbetriebnahme der Anlage. Das Programmieren der Schnittstellen zwischen Roboter und Software entfällt und es ist nur noch ein Programmierteam von Nöten. Sie können selbstständig mehrere Roboter unterschiedlicher Hersteller ohne Probleme in den Ablauf einfügen.
Wenn nun die Anlage stehen bleibt und der Anlagenbediener den Fehler nicht selbst findet, muss er nur noch die Instandhaltung anordnen. Diese kann sich mit dem SPS-Programmiergerät verbinden und ist in der Lage, sowohl das Roboterprogramm, als auch die gesamte Peripherie einer SPS-Entwicklungsumgebung zu debuggen. So kann die Produktion schneller weiterarbeiten und es kommt zu keinen Produktionsausfällen.
Neue Herausforderung
Eine Herausforderung ist nun noch die Bahnplanung. Diese übernimmt in den meisten Fällen nicht der SPS-Programmierer, da tiefere mathematische Kenntnisse vonnöten sind. Durch die SPS werden lediglich Befehle an die Steuerung gesendet, dort übersetzt und ausgeführt. SPS und Robotersteuerung sind über einen Feldbus miteinander verbunden. Dieser dient zur Kommunikation und somit zur Übertragung von Daten zwischen beiden Steuerungssystemen. Beispiele hierfür sind die Protokolle Ethercat, Profinet und Enternet/IP. Dabei übermittelt der Feldbus sogenannte Befehlkommando-IDs, mit Parametern der SPS (Roboterindex, Geschwindigkeit, Beschleunigung), an den Roboter.
Verkettung von Roboterbewegungen
Eine Roboterlaufbahn besteht üblicherweise aus mehreren Positionen, also mehreren Bewegungen. Wenn jede einzelne Position einzeln und linear angefahren wird, entsteht ein abgehackter, ruckeliger Ablauf. Um die Bewegung flüssiger zu gestalten, gibt es folgende Möglichkeiten:
- PTP-Bewegungen kommen zum Einsatz
- Punkte überschleifen
- Befehle verketten
Bei einer PTP-Steuereung (Point to Point) werden Anfangs- und Endpunkt einer Bewegung exakt festgelegt. Dabei ist allerding der Bahnverlauf zwischen den Punkten nicht im Programm definiert. PTP ist eine vergleichsweise einfache und schnelle Steuerungsmethode.
Überschleifen bedeutet, dass ein Punkt nicht exakt angefahren wird, sondern er lediglich als Anhaltspunkt für die Bewegung gilt. Durch diesen Punkt kann ein definierter Abstand ermittelt werden, mit welchem der Roboter einen Bogen fährt. Dadurch entsteht nicht nur eine flüssigere Bewegung, sondern auch eine höhere Geschwindigkeit.
Eine Befehlsverkettung bedeutet, die Befehle in einen Befehlspuffer des Roboters zu schreiben. Dadurch kann das Überschleifen im Vorfeld einer Bewegung berechnet werden. Um zwei Befehle miteinander zu verketten wird der Execute-Eingang des nachfolgenden Befehls mit dem Busy-Ausgang des ersten Befehls verknüpft.
Übersichtlicher Arbeitsalltag dank SPS
Trotz einiger Herausforderungen bei der Bahnplanung des Roboters erleichtert eine SPS den Alltag eines Anlagenbauers enorm. Er benötigt nur noch ein Programmierteam und ist nicht mehr auf die Hilfe vieler Spezialisten angewiesen.